Point White Drive Plans
After completing the Diploma of Architecture at the Architectural Association School of Architecture in July 1993 my wife and I traveled to Bainbridge Island for a one-month house-swap. The island is off the coast of Seattle and is accessible by ferry from downtown. There are numerous architecture firms in Seattle and this opportunity to visit the Pacific Northwest came with several job interviews. The economy in the early 1990s was depressed and there was high unemployment among architects. We returned to London to work for another two years. It was during this two year period that I completed the design and construction of a Functional Brain Imaging Laboratory for the Welcome Trust in Queens Square, London for the Royal Institute of Neurology while employed by the Devereux Partnership. In 1995 I completed my RIBA part three examination and made plans to relocate to Bainbridge Island. We initially looked at existing homes to purchase for our family. We found a 3 acre piece of land on the south end of Bainbridge Island that had magnificent views of Rich Passage, part of the Puget Sound that comprises the body of water off of the south end of Bainbridge Island.
Drilling for Water- a first step
The prospect of designing and building our own home came with a great deal of responsibility and risk for the development of the land. Since there is no utility water supply to many locations on Bainbridge Island it was necessary to drill a water well. In order to purchase the land, the feasibility of striking water had to be explored prior to making a offer on the land. Hence, a well drilling rig required access to the low point on the land which meant that we had to cut some trees and perform some initial clearing. The clearing of trees required us to obtain a clearing permit. We had the permission of the land owner to clear a limited number of trees in order to drill an exploratory water well. Once we struck water we determined that there was more than adequate water pressure to supply our house as well as one or two other houses. The water we found was also clear of any calcium deposits or other contaminants that can often require domestic water to be treated on-site.
After having accepted our offer for the land, the owners gave us permission to carry on clearing the land of the trees that we intended to mill and to have kiln dried for our house's decking material, siding material, beams, posts, interior trim and soffit material. The logger who cut the trees required a beam schedule from me in order to determine the length of the logs that were required for our house's timber package. The design for the house had evolved sufficiently for us to provide him with the information he needed in order to start making the timber from the logs. We had originally intended to design a timber-framed home with traditional exposed beams and brackets that are common to the craftsman style of the Pacific Northwest. The less-expensive option was to balloon frame the house in conventional house construction methods and to have a limited number of exposed beams and columns with custom bracketry to complete the joinery. Therefore, all of the conventional framing material required for the "two by" construction was purchased from the lumberyard and all of the beams and columns and all of the decking, siding and soffit material was provided from our milling operation.
After clearing the land and drilling the freshwater well, the need for a septic design was next. We hired a civil engineer and a septic field designer to provide us with an application to the department of health for our house's septic plan. This was a risky undertaking because gravity fed drainfields were becoming a liability to many home owners and the town was contemplating a ban on this type of septic design. This was because the ground was quite often not permeable enough to allow for the percolation of human waste into the ground. Our septic designer added a great deal of sandy soil to the design of our septic field which was perforated pipe encased in granite gravel. Soon we had a permitted septic design for our piece of land and that concluded the contingencies that we allowed for and the purchase of our 3 acre lot was completed in December 1995.
What remained for us to do was to complete a Wildlife Survey of our land to search for any bald eagles nests or other wildlife that could impede our construction permit. A wildlife specialist was employed to come in and do a Wildlife Survey for us. This resulted in no obstacles to our building permit and we were soon able to begin interviewing contractors for our house project. At the time that I was beginning to design the house, I was employed on a $160 million prison project for the State of Washington by NBBJ. I had completed a three-dimensional framing model of the house for the purposes of quantifying my timber package. A friend of mine who was an architect at the Miller Hull company asked if I could use some help with the construction drawings. Peter Wolff became an employee of the construction contracting company that I had engaged to build my house. Peter carried out all of the construction drawings for the house during the 1996 timeframe and construction began in 1997. The Reijnen Company was the builder of the house. The size of the house as defined in my three-dimensional framing model was reduced in order to achieve a budget of approximately $300,000. Peter was able to import my three-dimensional framing model into AutoCAD and to produce the various two-dimensional sections, plans, and elevations of the house.
Designing a House while working as an Architect- Day Job / Night Job
Design and Construction of the house during this initial period while employed by NBBJ was a full time occupation. During the period of time that I was designing the house, I was also part of large team of architects designing the Stafford Creek Corrections Center in Grays Harbor, Washington. I was also briefly involved in Swedish Hospital Phase 5 Surgery in the early days of the house project. Also during this period, the contents of our home from London was shipped in a 40 foot shipping container to our rental property on Bainbridge Island. We had arrived in Seattle in September of 1995 and our newborn son turned one on October 1. Just prior to starting construction of the house in April 1997, Josephine our third child was born to us on December 30, 1996. Presented with the same opportunity, in hindsight – I'd've had less on my plate.
The design of the house was driven largely by the geography of the site and the enormous Douglas firs that paced across the property, controlling views out of the site to the south, out to the body of water that presented us with so much maritime traffic, the sound of the ferries, the naval ships and the sounds of the sea lions in the water calling out below. The presence of and the movement of ships past our house was calling for the nautical architecture that I embraced so wholeheartedly with the south elevation of the house. The views out of the site and the southerly aspect of the property were what steered me towards the large expanses of glass. The large rectangular forms that bulge briefly through the curving wall of the south elevation created an animated interactive space that brought the outdoors in and the indoors out. During the summer, the curving deck, which wrapped around the major living spaces was a space which was next to the large plates of laminated glass that separated us from the interior of the house and frequently created an interesting hybrid space that blurred the lines between the two.
Many of the components of the house were owner provided. As discussed previously, all of the decking, siding, interior trim, soffit material, beams and posts for the house were owner provided. In addition to that, all door hardware, appliances, electrical fixtures, and balustrades were owner provided to the contractor. The deck was constructed of custom milled cedar decking which dimensionally had to be able to be bent to match the radius of the curve of the South Wall. This resulted in 3 inch wide decking material. All of the floorboards of the deck workbench in order to follow the bending cedar siding of the vertical surface. The handrail on the balustrade also had to curve with the south elevation. This material was bolted to custom stanchions that were hot dipped and lag bolted to a curving 2" x 12" facia board that terminated the 2" x 8" joist ends of the deck. In order to stabilize the curving balustrade, outriggers which hold the balustrade outwards to compensate for the inward force of the tensioned aircraft cable were attached to periodic cantilevering joists.
Another owner provided item was the detention pond which collected all of the storm water off of the driveway and all of the storm water off of the roofs. The detention pond was located to the east of the house and was frequently filled with water in the Pacific Northwest climate that measured rainfall in feet not inches. There was an excessive amount of organic debris that was blown off of the Douglass firs that collected on the roofs and would normally clog gutters but for the gutter-less design of our storm water system. All of the roofs were standing seam metal Galv-alum roofs. The Douglas Fir leaves which collected on the roof were washed down hill across the cascading slopes of standing seam metal. A French drain surrounded the house and egressed water into the detention pond through under ground pipes. The French drain was entirely constructed from Granite drain rock. This granite drain rock apron which surrounded the house created a 12 foot surface transition from green grass to granite rock. The organic debris from the roofs was easily collected at ground level periodically while the water continued on to deposit in the detention pond.
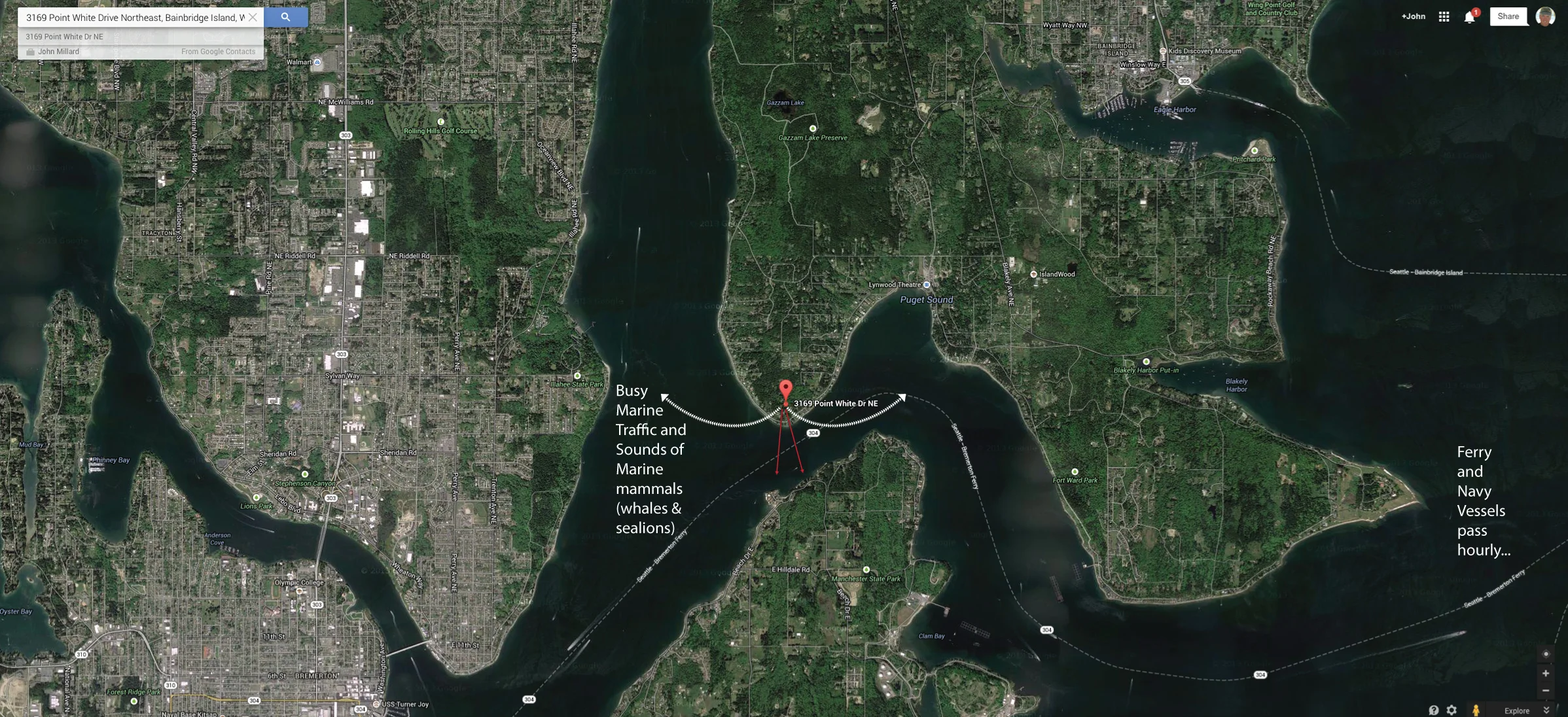
Location Map: Bainbridge Island, Washington- Point White
Points White is a peninsula on Bainbridge Island that has a strong southerly aspect, with views of Port Orchard Bay. The ground rises abruptly out of the passage to a height of 100 feet above sea level where the house is located. There is a significant amount of marine traffic that passes through Point White on an hourly basis.
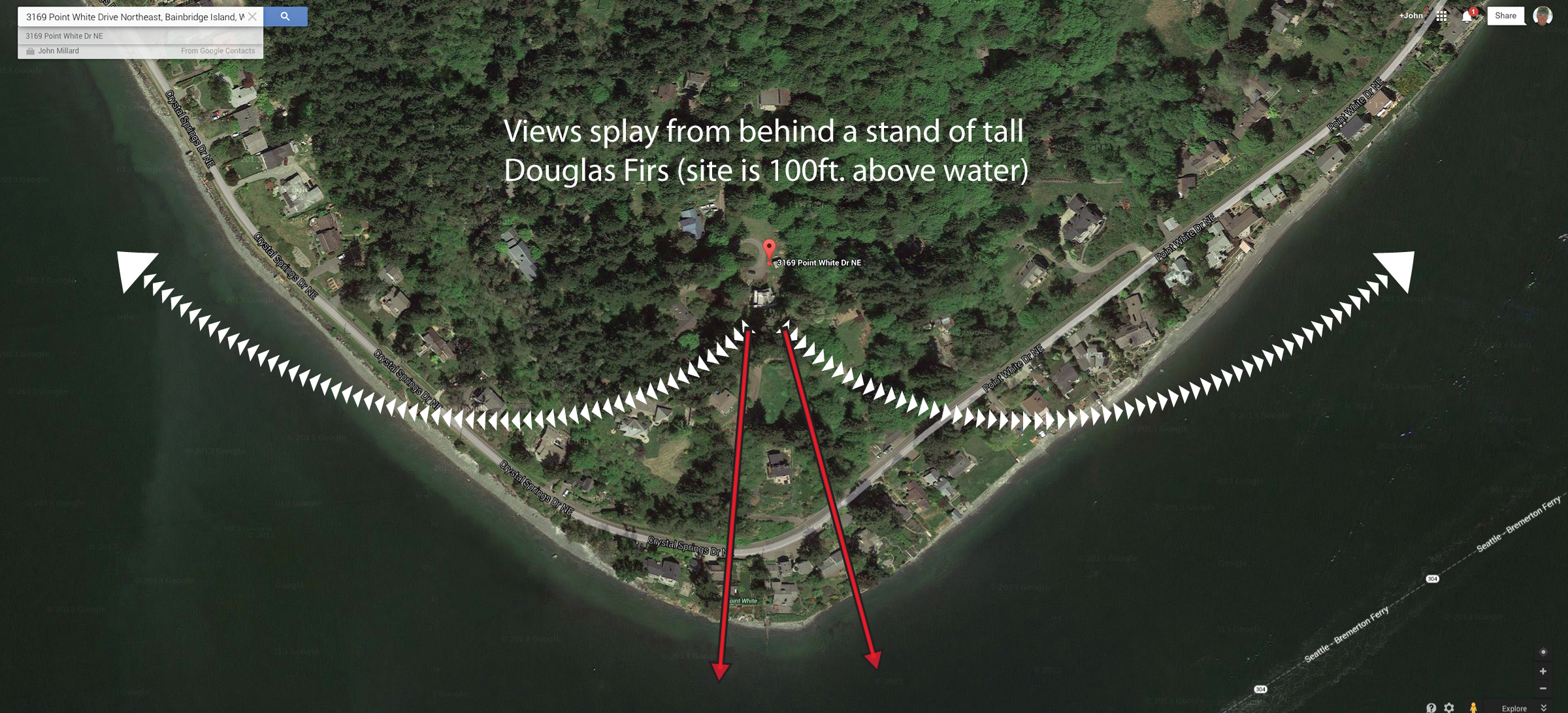
Point White Drive is over-looked by an old growth Douglas Fur and Western Red Cedar Forest.
Access to the homesite is up a very steep driveway that is a right-of-way. There are strong views of the home site from this right away. Views out of the site from a height of 100 feet above sea level are able to see ferry and naval traffic including the occasional aircraft carrier.
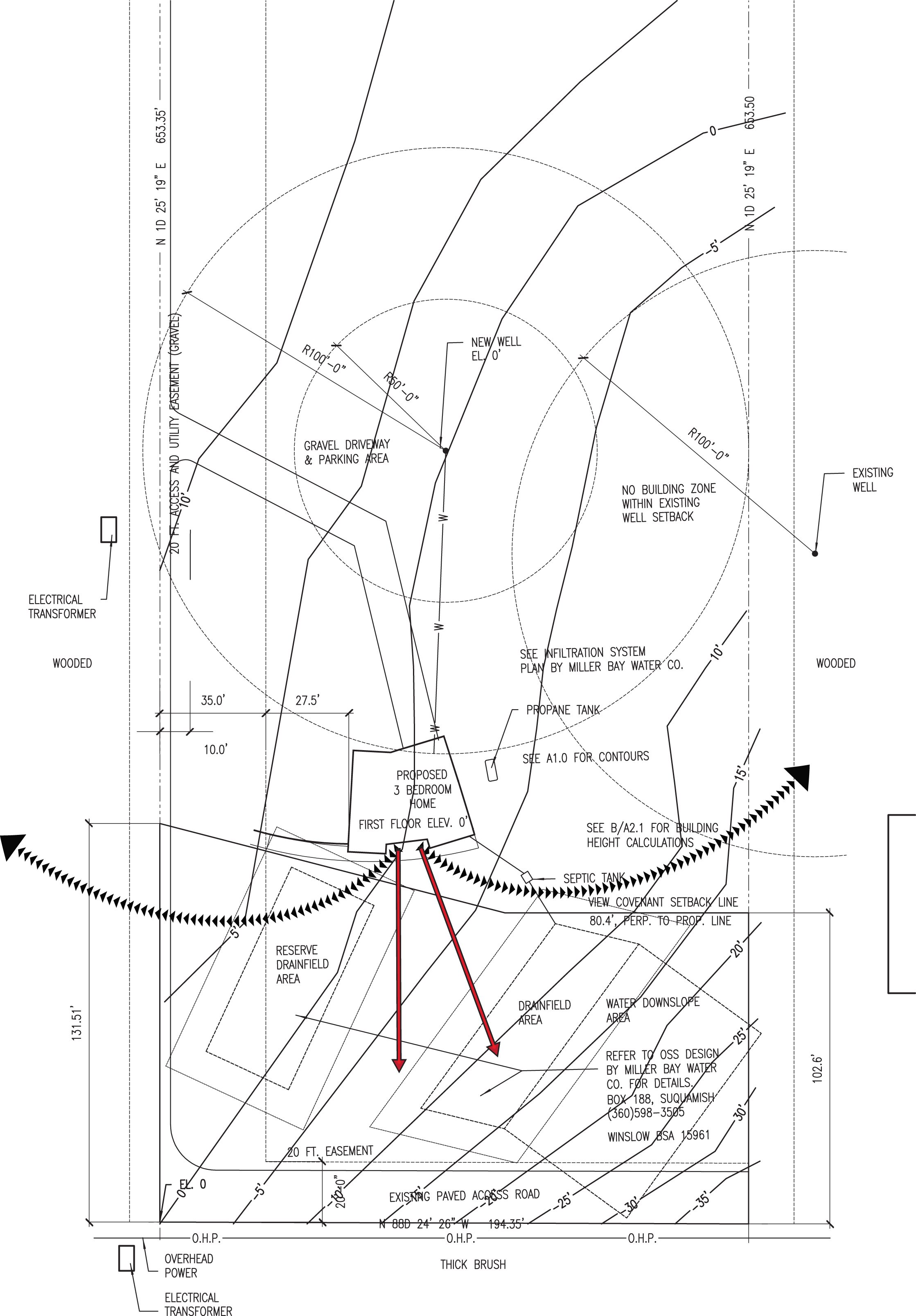
Site Plan: Adjoining owner required a view covenants to protect their views of Rich Passage
3169 Point White Drive is a 3 acre site that consisted of extensive Douglas Fur and Western Red Cedar trees. There was a very large western red cedar tree directly on the homesite which was milled for all of the siding, decking and soffit material for the house. The house uses a gravity-fed septic design that enabled the front yard of the house to be clear of any appurtenances in accordance with the view covenant with the next-door neighbors. Additionally, not shown on this plan is the avenue of Douglas for trees that pace across the site from the west to the east. These trees which were limbed up to a height of 50 feet controled views out of the site from the house.
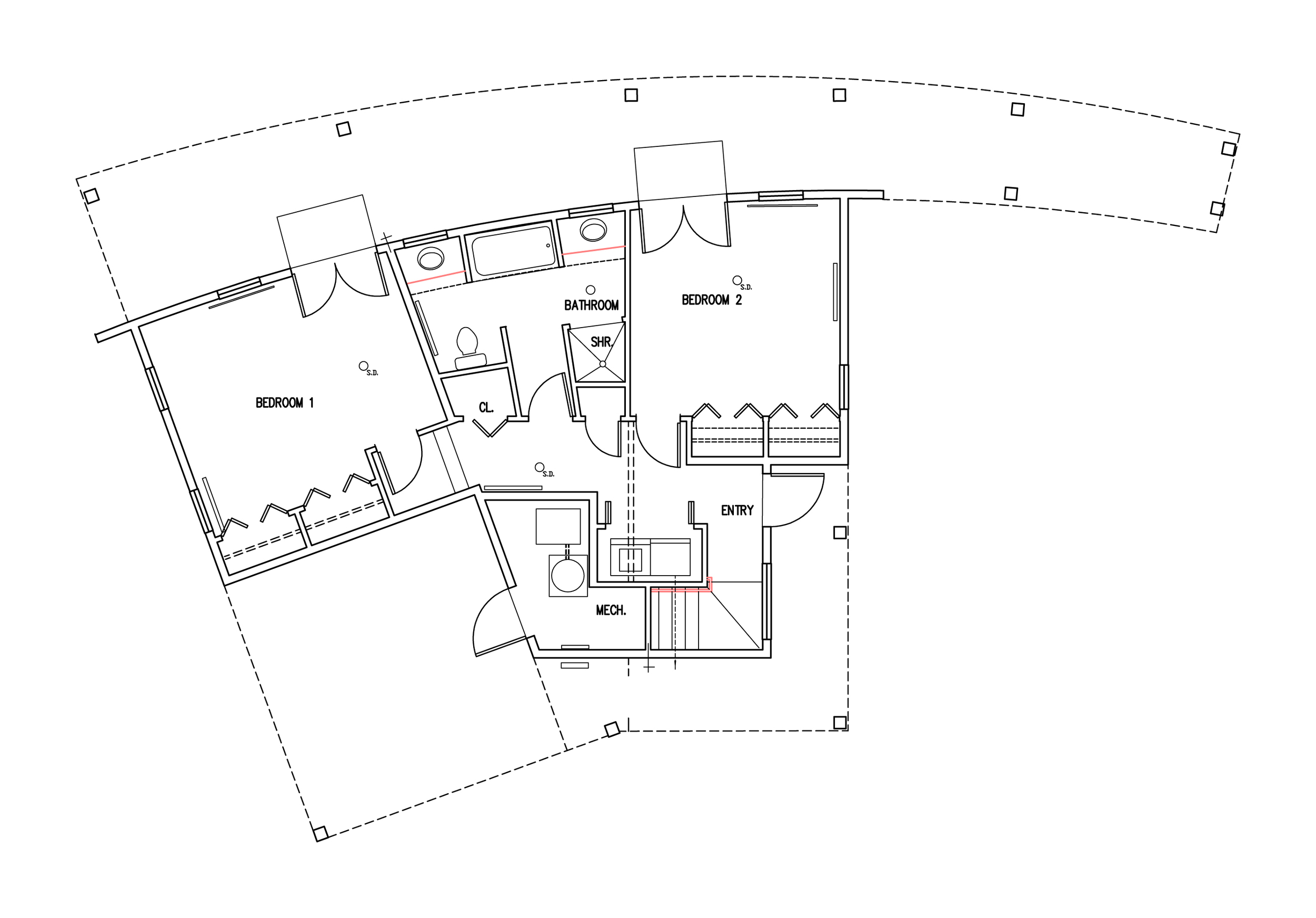
Ground Floor Plan- children's bedroom level with bathroom and utility room.
The ground floor of the house has its own entrance under a covered soffit that is accessible from the carport. The gas boiler, well-controlled and electrical panel are accessible from the carport but hermetically sealed from the occupied spaces of the ground floor.
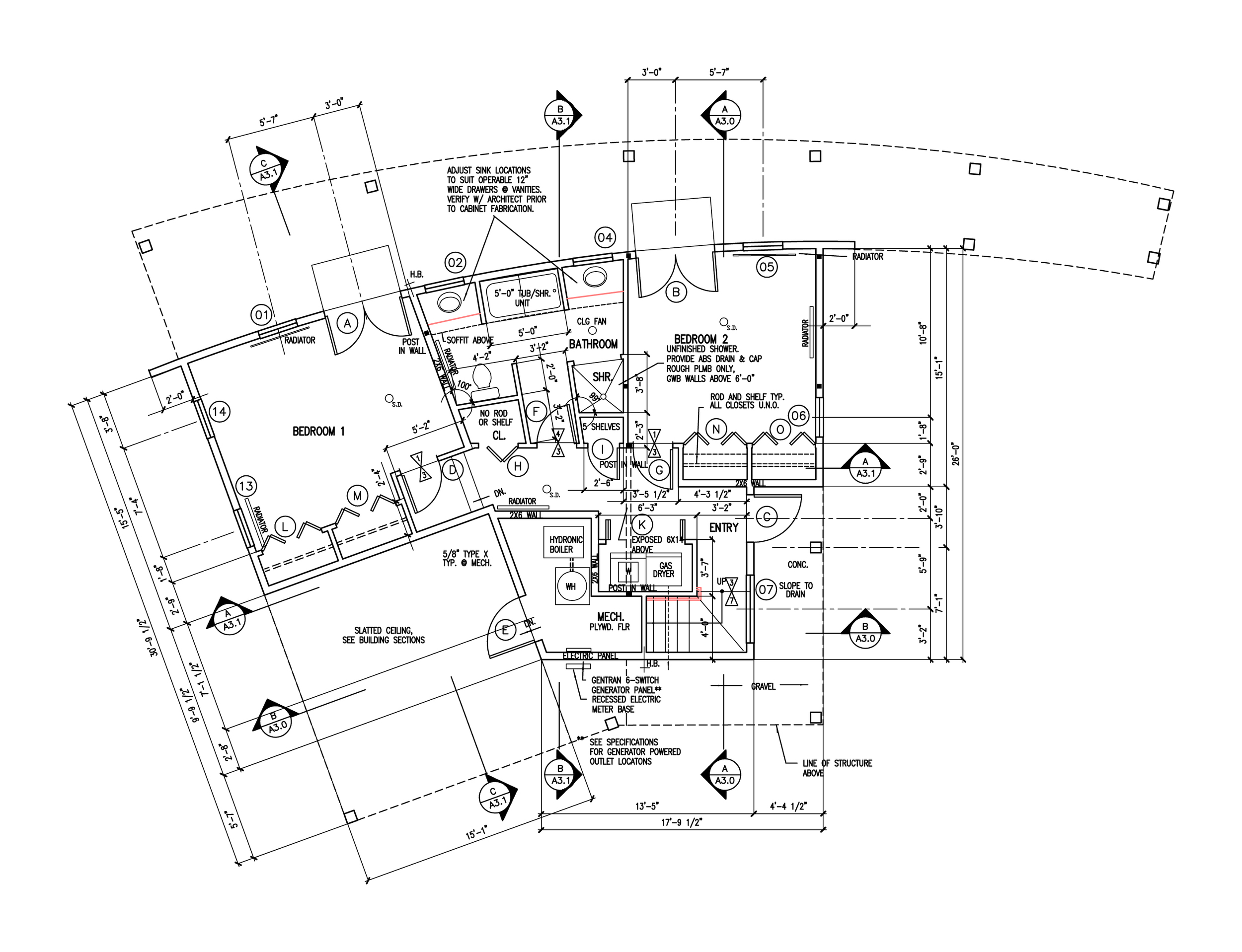
Working Ground Floor Plan- Seismic Zone 4
It is on the ground floor where the perfect curve of the south elevation is plotted using a cantilevering floor joists are cut along the curve using a snap line. These joists are held down to the concrete foundations using seismic holddowns specified by a structural engineer.
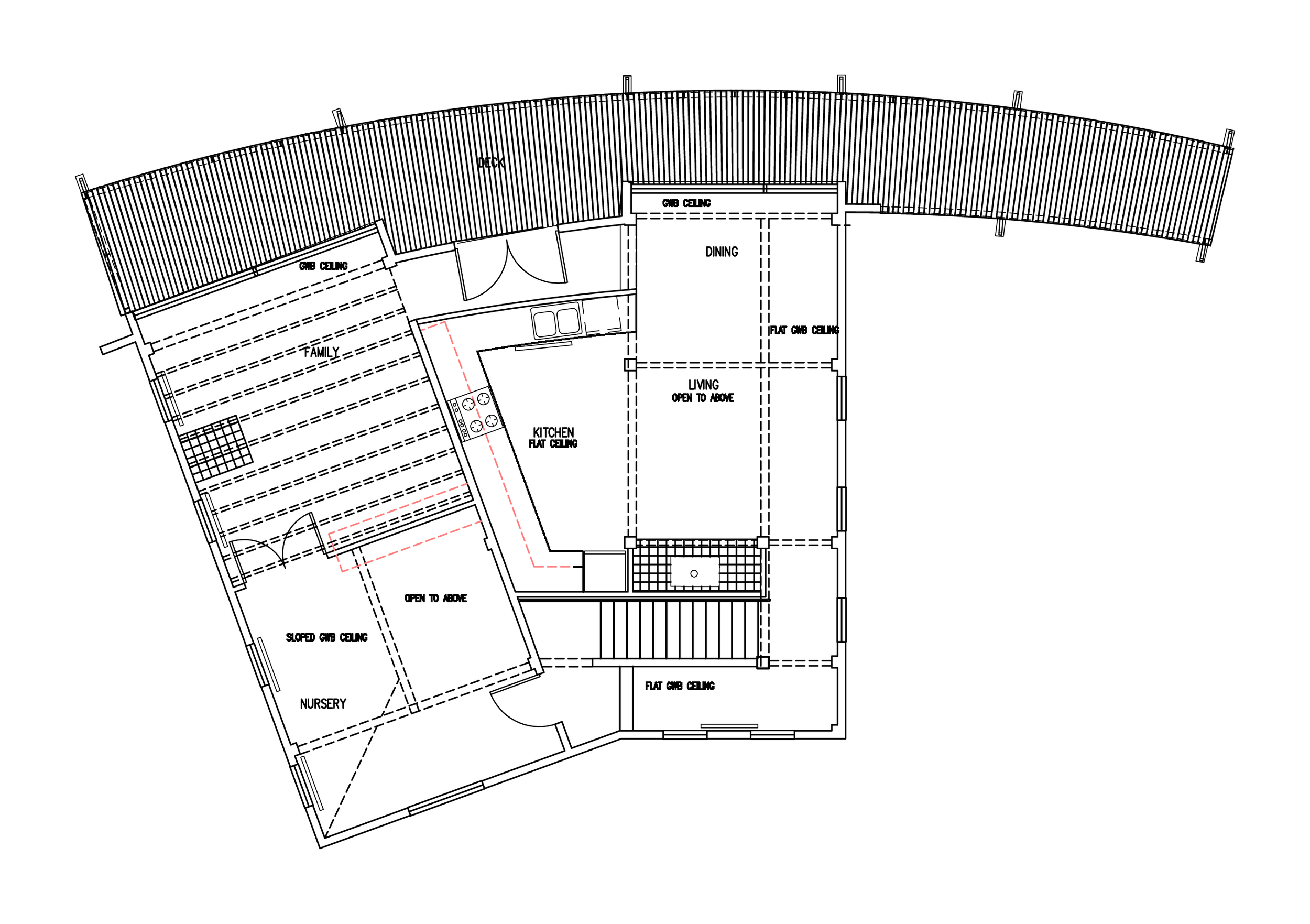
Second Floor Plan- Formal Entry and Uncovered Deck
The semi public spaces of the ground floor are comprised of two separate building volumes each pointing out into the landscape in a different direction through the curve of the south wall. These two spaces create very large bay windows in the south wall. The windows are toughened, laminated glass.
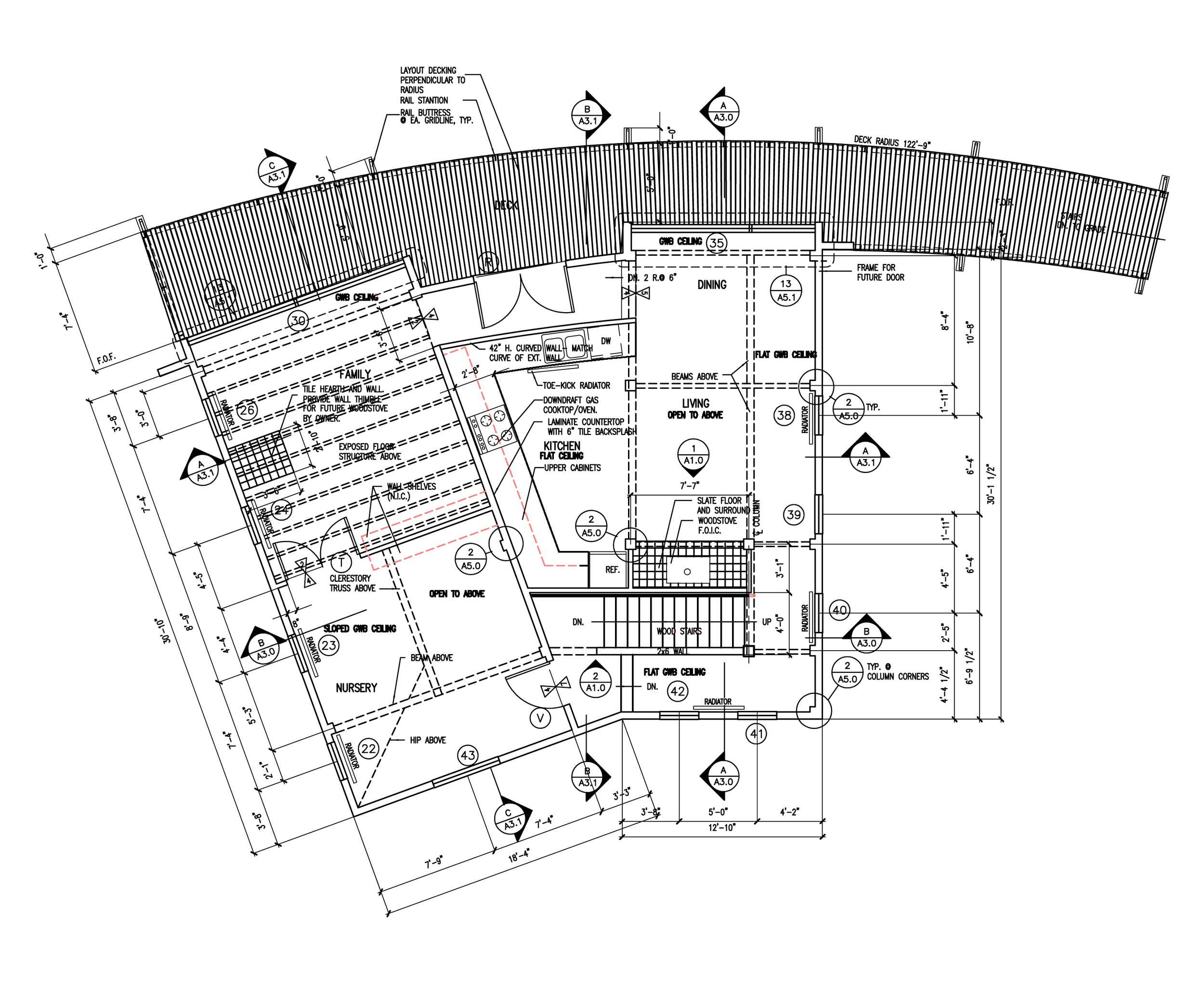
Working Second Floor Plan- two separate levels with double height spaces over each.
The second floor is broken into two separate levels, that step occurs around the kitchen shape. As a result of this step, the living spaces of the house, follow the natural slope of the site.
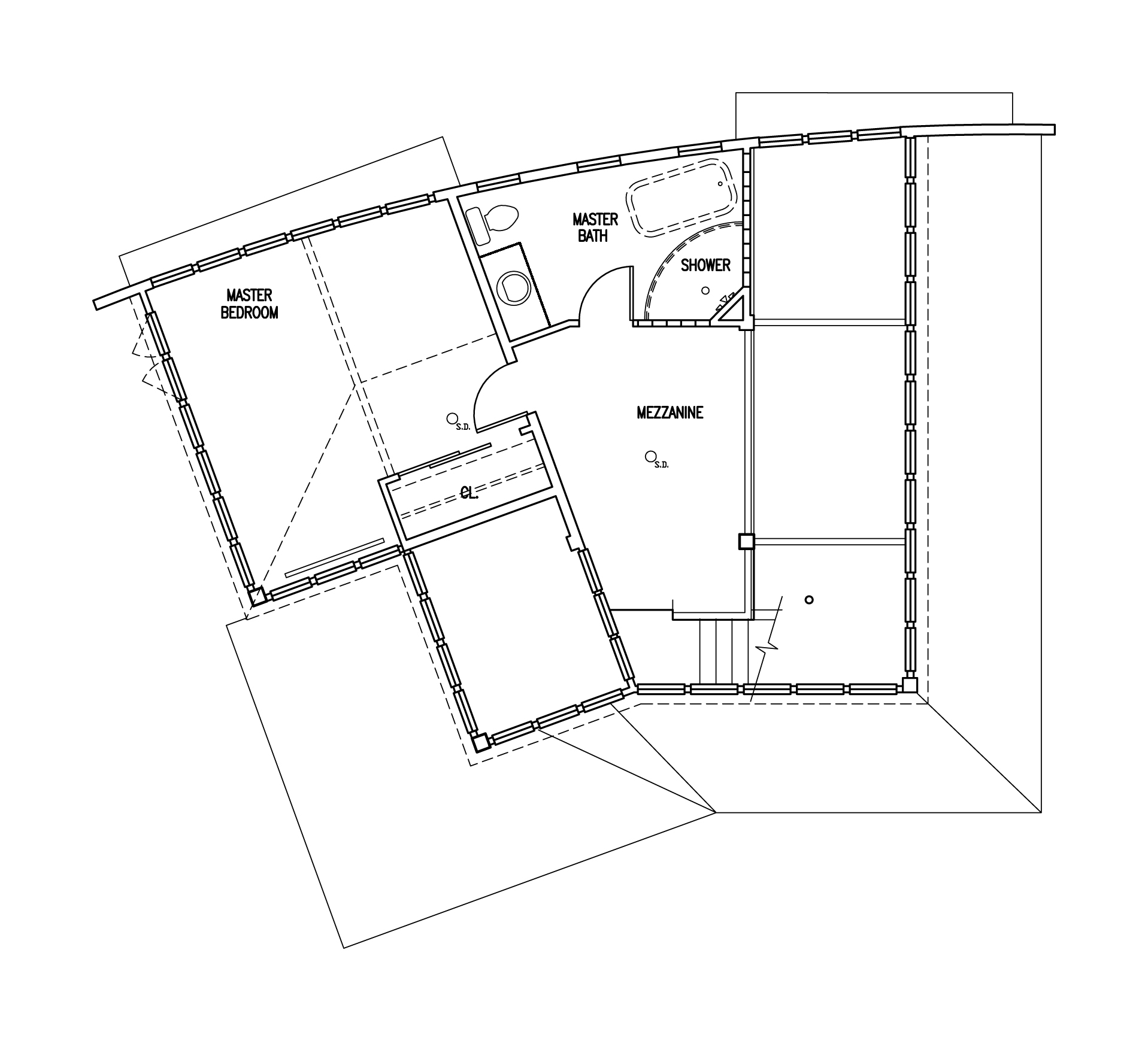
Third Floor Plan- surrounded by clerestory windows
The master bedroom suite is located on the third floor. It is surrounded by sixty-five 12" x 12" clerestory windows. Some of these windows are operable and they allow warm air to escape from the high volumes of this space during the summertime. They provide a high degree of natural light in the house year round. The house complies with energy code for glazing-to-opaque wall surface ratio of 30%.
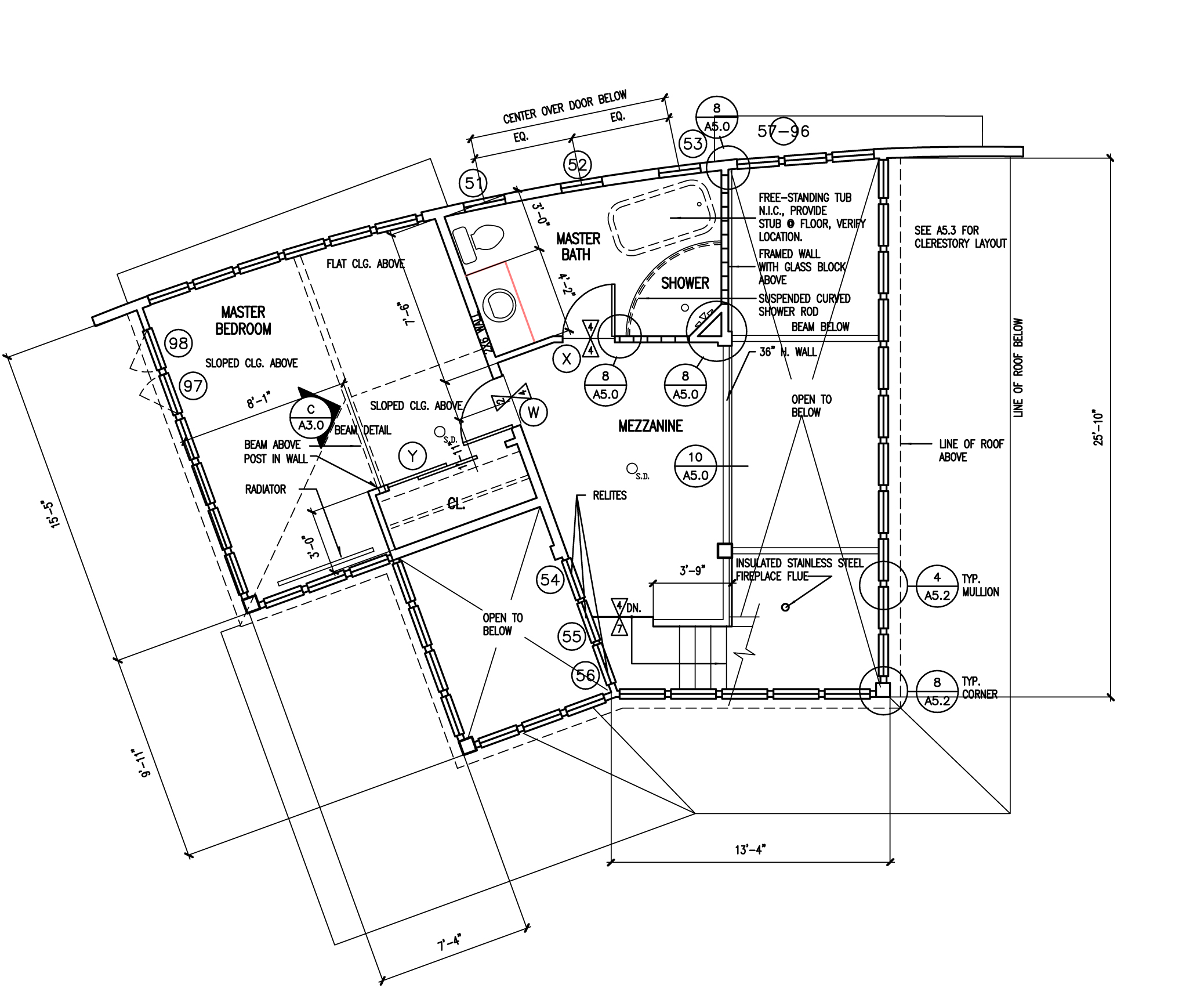
Working Second Floor Plan- the framing of this level was tricky due to the tight tolerances of the roof design.
Framing of the third floor master bedroom suite required some exposed beams and some strong lintels to carry the load of the roof above the clerestory windows. Each clerestory window is separated by a pair of continuous 2"x 6" wall studs that continue from the floor plate through to the top of the wall
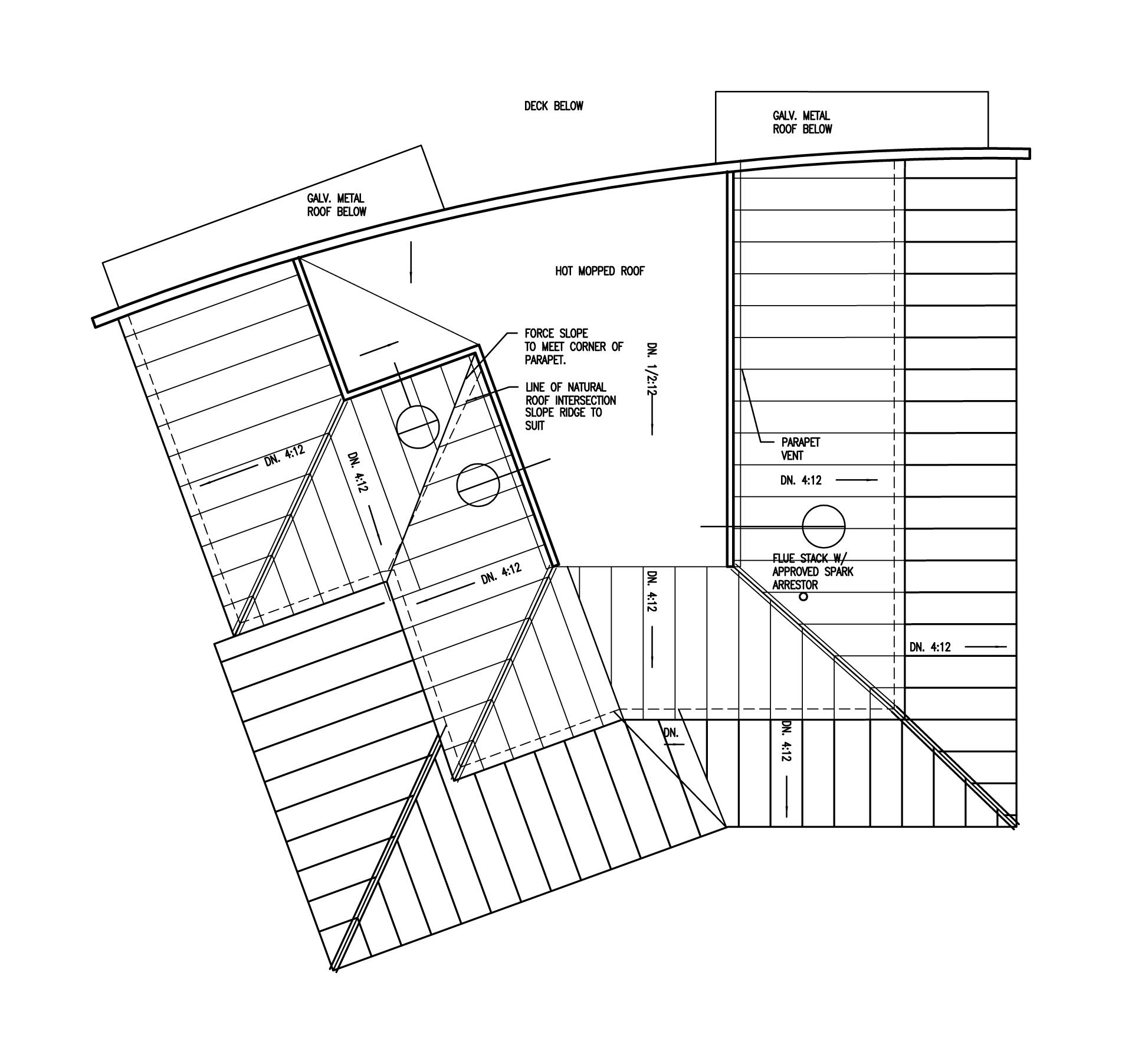
Roof Plan- Standing Seam Metal Roofing (Galv-Alum)
The climate in the Pacific Northwest measures rainfall feet and the wind on this end of the island takes the full brunt of the prevailing winds from the south. The foliage that blows off of the Douglas Furner trees is a significant accumulation of organic material on the roof. For this reason there are no gutters in the rainwater design for the house. The concrete foundations of the house are backfilled with soil that allows for a French drain. The drain is lined and egresses water into a detention pond on the east side of the house. The wind-driven organic matter from the trees accumulates on the ground where it is driven by the rain water off of the standing seam metal roofs.
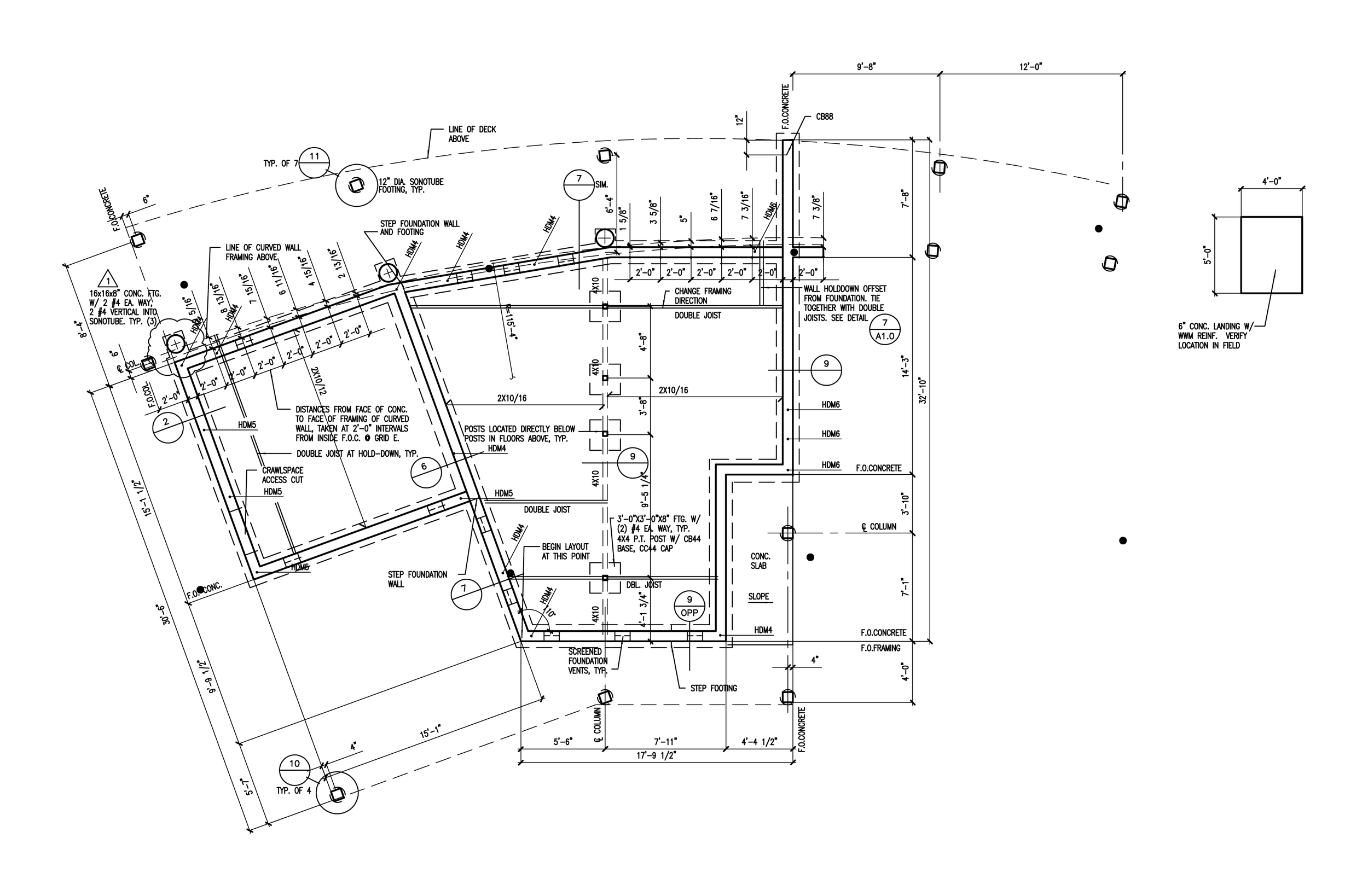
Foundation Plan- Designed for a Seismic Zone 4
The house structure performed very well throughout the several 6+ magnitude earthquakes that occurred during the four years that we lived in the house. There were no cracks in the drywall, which were designed with generous rebates where they meet the framing. Additionally, the major structure of the house is supported on posts which allow for some movement above.